6 New CAD Technologies (and When to Use Them)
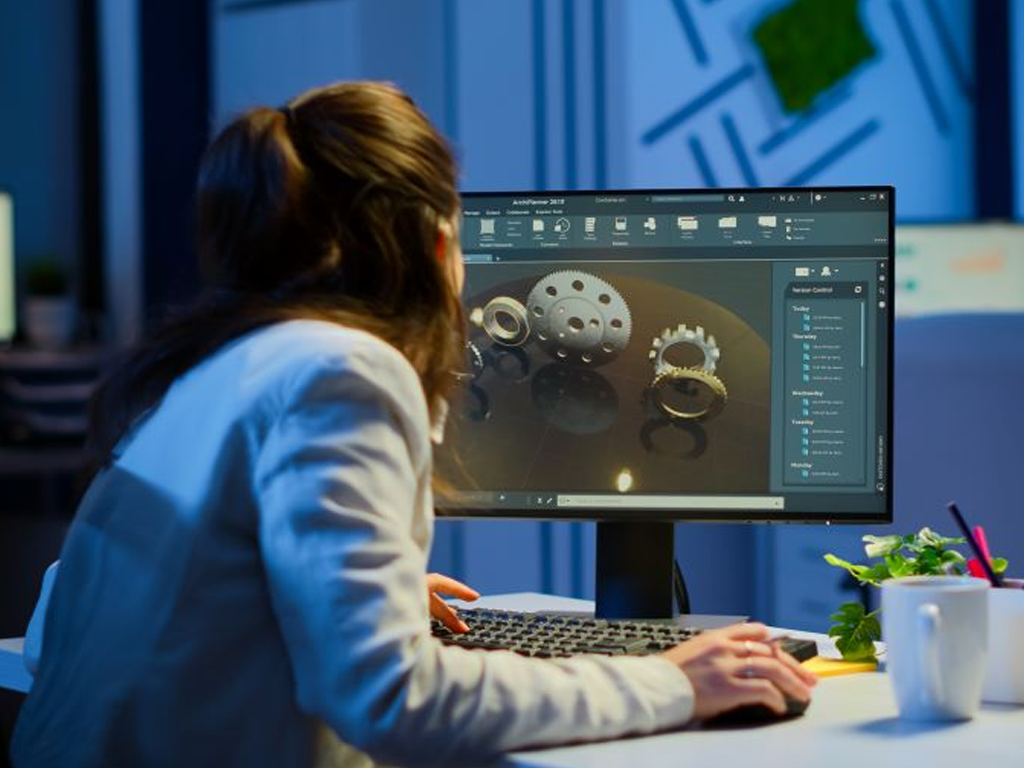
Editor's Note: This post was originally published in 2017, it was updated in Dec. 2022.
When I started studying engineering, CAD usually stood for computer-aided drafting. Shortly thereafter, as 3D modelers became more popular, the term colloquially became computer-aided design. Now, in 2022, I’m convinced we’ve arrived in the age of true computer-aided engineering, or CAE.
Why are we now in the age of CAE? We’re seeing the integration of many technologies that elevate 3D modeling tools, transforming them from a convenience to a design assistant that participates in our product-development process.
This idea expands the groundbreaking work in additive manufacturing (AM) by Andreas Vlahinos. Engineering is different from design in that engineering applies math and an established body of mechanical theory to the development of new products.
Let’s look at six new and emerging 3D CAD technologies (and when to use them):
-
Topology Optimization and Generative Design: These tools represent the application of artificial intelligence (AI) and machine learning (ML) to the design process. With topology optimization, you can find a single solution for an engineering problem. Generative design generates numerous potential concepts at the beginning of the design cycle.
-
Additive Manufacturing: Closely related to 3D printing, additive manufacturing helps manufacture parts that are lighter, with more complex geometry and fewer components, than what’s possible with traditional subtractive manufacturing techniques.
-
Real-Time Simulation: With real-time simulation, engineers can perform structural, thermal, modal, and fluid flow analyses of our models. The results update on the geometry as designs are in progress, providing immediate feedback of how changes will affect the model.
-
Model-Based Definition (MBD): Model-based definition, or MBD, is an annotated 3D model that contains all the information needed to manufacture and inspect a product. In MBD, you capture the dimensions, tolerances, notes, symbols, surface finishes, and other information that define components and products in the model, as opposed to a traditional 2D drawing. Rather than sharing a drawing, you can share the model, either in its native format or a neutral STEP format. This is how you start on a path to becoming a model-based enterprise.
-
Behavioral Modeling: Feasibility and optimization studies allow us to build our design intent into models. We can vary any dimension or parameter within a specified range to meet design constraints and minimize or maximize another measure, such as mass.
-
Ergonomic Design: Designing for ergonomics is increasingly becoming more important to product designers and engineers. Why? Just as humans don't come in one shape or size, neither should form, fit, or function. With new capabilities in Creo 9, you can account for the uniqueness of users as you design products for them. With ergonomic designs, you put your customer at the center of your design process.
How to Use Emerging Technologies in Your Design Project
What does it look like when you combine these emerging technologies? Imagine you’re starting a new design project. Your workflow could look like this:
-
You develop design requirements for the envelope, keep in/keep out volumes, boundary conditions where your product will interface with other components, and load cases.
-
Based on the requirements, you develop a multibody model to define starting geometry (initial envelope), preserved geometry (volumes that must be maintained), excluded geometry (volumes that must be avoided), and undesignated bodies (geometry that facilitates creation of boundary conditions and load cases).
-
You develop topology optimization and/or generative design studies to let Creo formulate potential solutions.
- Topology optimization helps you find the best solution, based on whatever criteria and manufacturing method (CNC machining, injection molding/casting, or additive manufacturing) you specify.
- Generative design studies are performed in the cloud leveraging the Atlas SaaS technology. The study produces numerous potential design alternatives, many of which your team probably would not have conceived. You apply Pareto methods to pare down the results and select an initial concept.
- You set up a real-time simulation so you can see how critical analysis measures change as you refine the design.
- You initiate a design exploration session focused on ergonomic design so you can branch off into design alternatives that better suit your intended customer.
- You refine the design by using lattice features to reduce the mass for components that will be produced using additive manufacturing. The lattice feature dimensions can be used as design parameters in feasibility and optimization studies.
In this workflow, your CAD package has performed most of the heavy lifting throughout the design process, from concept through detailed design. Simulation and optimization are performed in parallel with design work, rather than at the end of the process.
Emerging Technologies in Creo 9
CAD tools have evolved from simply following our instructions and facilitating geometry creation, to a quasi-independent engineering assistant. Now is an exciting time to be in product development.
Are you familiar with all these emerging technologies? Would any of them benefit your design process?
Creo 9 introduces a wide variety of customer-driven improvements to help make every day more productive. These include new tools for managing, manipulating, and understanding CAD models, as well as enhancements to capabilities in design-for-ergonomics, model-based definition (MBD), simulation, generative design, and both additive and subtractive manufacturing. Learn more about Creo 9 here.